- Author
- A.N. Other
- Subjects
- Ship design and development, Naval Technology, Infrastructure and Facilities
- Tags
-
- RAN Ships
- HMAS Canberra III, HMAS Adelaide III
- Publication
- December 2021 edition of the Naval Historical Review (all rights reserved)
By Phil Baldwin, CEng CMarEng FIMarEST
Background
In November 2007 the Australian Department of Defence procured two ALHDs through BAE Systems Australia. The platform was based on the Navantia (Spain) designed Juan Carlos 1 which was built for the Spanish Navy. The hull and the majority of the machinery and platform systems were built and installed by Navantia S.A. in Spain. The superstructure, communications and combat systems were fitted out in Australia. HMAS Canberra, Navantia hull number 213, entered service in October 2014 followed by HMAS Adelaide, hull number 214, in October 2015. The vessels were built to Lloyd’s Register (LR) Naval Ship Rules (NSR) 2005 and are in-class with LR.
The main machinery is a combined diesel/turbine-electric drive plant that provides power for the vessels two pods and general electrical power requirements. There are two diesel generator sets powered by Navantia-MAN 16V 32/40 diesels each rated at 7,450 KWe 6,600V, 60 Hz 3 phase and one GE LM2500 gas turbine generator rated at 22 MWe. The electric drive system connects to the port and starboard pods, Siemens Schottel Propulsors SSP 10, input power 11 MWe, prop speed ahead 10 to 176 rpm, astern 10 to 88 rpm. The general, low power, electrical system of the ships is provided through conversion machinery at 450V, 60Hz, 3 phase.
From the outset, the staff of Canberra made adverse comments about the levels of vibrations in the ship as being uncomfortable, in spite of the ship having the LR notation for Crew and Embarked Personnel Accommodation Comfort 2 (CEPAC2). The crew of Adelaide made similar complaints when she entered service. The Commonwealth raised the issue with the shipbuilder, however the claim was rejected based on the premise of the award of the notation and acceptance that the contracted requirements for CEPAC2 had been met.
Service Experience and Investigation
During 2016 problems associated with excessive background structural vibration levels began to manifest themselves in a number of ways in both ALHDs. Cavitating propellers were suspected as being the source of the vibrations. Underwater inspections of the propellers in both ALHDs found cavitation erosion of the propeller blades. The erosion was at various stages of advancement but was sufficiently severe to cause concern about their long-term material viability, noting propellers should last for the life of the platform. Additionally other material shortcomings in the platforms were affecting their overall reliability.
It was decided to establish a dedicated team to manage and deal with a significant number of issues with the ALHDs. The Transition and Remediation Project (TaRP) commenced at the beginning of April 2017. The small handpicked team consisted of up to eight engineers from various industry service providers with a similar number of Commonwealth employees to provide commercial and administrative support. With a clear mandate, budget and project timeline, the TaRP remediated the majority of issues or initiated solutions for sustainment to manage over the longer term. Having successfully achieved its aim the TaRP closed in late 2020.
Adelaide was dry-docked in May 2017 to conduct essential maintenance including five year servicing of the pods and to fit new propellers (original 3-bladed design). A similar work package was conducted in Canberra in Spring of 2017. Figures 1 and 2 show Canberra’s pods and propellers three years later, prior to replacement. With a clean hull and known machinery condition extensive trials were conducted in the ALHDs to identify and quantify the forces that were exciting the hull. The TaRP actively engaged the Commonwealth’s hydrodynamic and structural specialists in the Defence Science and Technology Group (DSTG) and Naval Technical Bureaus [now Directorate of Naval Engineering (DNE)] to provide advice regarding the problem. The Commonwealth contracted the vibration surveys, hull pressure measurements and propeller observations to LR’s Technical Investigation Department (TID). Navantia, as the ship designer, engaged a Spanish based company TSI to conduct separate vibration measurements and provide expert advice.
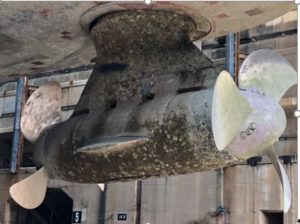
The vibration surveys determined that the natural frequencies of the structure on 2 deck and other key locations wereexcited by the propeller blade passing frequency (BPF) over a 2.5 Hz frequency range with the dominant frequencies between 7.5 and 7.8 Hz. The natural frequency of the complete pod assembly was coincident with that of 2 deck. An assessment of each platform against the requirements of CEPAC2 found that neither met the criteria for the award of the notation. Propeller observations identified the development of erosive cavitation on the blades in areas where erosion damage existed previously.
Analysis and the 4 Bladed Propeller Study
The substantial amount of data obtained during sea trials was subject to extensive analysis by the Commonwealth and the ship designer. In June 2018 it was accepted by all parties that the primary cause of the excessive vibrations was a combination of thrust variations between the pod forward and after blades and propeller cavitation. It was agreed that the best solution was to redesign the propellers with more than three blades as this solution would:
- Smooth the wakefield between the forward and aft propellers and thereby reduce the thrust variations;
- Lower the speed at which the resonant frequency occurred and therefore, reduce the power (force) available to excite the system.
To determine the optimum solution, it was agreed to undertake a study to redesign the propellers, which subsequently became known as the 4-bladed propeller study. The Commonwealth contracted the study through Navantia, given its role as the platform designer and system integrator. As a consequence of differing approaches to propeller design between Navantia and Siemens the Commonwealth agreed on two different design teams, one consisting of Navantia and MARIN and the other Siemens with SVA Potsdam. Siemens advised it was going to pursue an optimised 3-bladed propeller design.
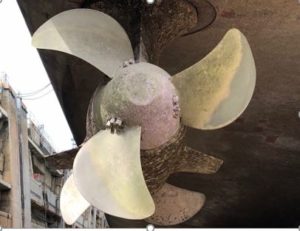
Before the commencement of the study the data obtained from Canberra’s trials, most notably the propeller observation videos and environmental conditions, were supplied to MARIN. During the ALHD acquisition stage Navantia and Siemens had engaged MARIN to undertake limited design, modelling and tank testing work on the pod aft propeller. Using this original model of the pod and three bladed propeller
configuration MARIN undertook tank testing. By adjustment of the model coefficients and scaling factors it was able to replicate the cavitation observed at sea. This provided a high degree of confidence that subsequent testing of the new propeller designs would give results that would be close to the expected propeller performance once operating in the ships.
The design study commenced in May 2019. The Commonwealth provided the acceptance criteria for the new propellers as well as a prioritised list of design requirements that needed to be achieved by the successful propeller design. Furthermore, it was agreed that testing and evaluation of both propeller designs would be undertaken by MARIN at its facilities in the Netherlands using its approved and tried procedures and processes. Navantia was required to evaluate the two designs against the design criteria and provide a recommendation to the Commonwealth on which design best met the criteria and should be taken to production.
Between May and the end of August 2019 both design teams undertook detailed design of their respective propeller proposals. Models were produced and testing and evaluation undertaken as MARIN’s facilities. Each designer produced a detailed design report covering all aspects of the design, the results of the tank testing and its compliance with the Commonwealth’s requirements.
Siemens raised concerns about the pod shaft dynamic vibratory response with 4-bladed propellers. To provide independent analysis of the system response the Commonwealth through Navantia engaged LR TID to undertake finite element modelling to analyse the dynamic response of the pod shaft to Siemens computational fluid dynamics calculated thrust forces for both designs. On completion of this extensive study it was concluded that the predicted shaft dynamic response with the 4-bladed propellers was satisfactory.
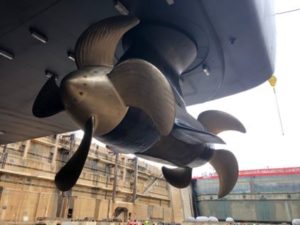
A design review meeting was held with all parties and the results presented. Navantia concluded that the 4-bladed propeller best met the Commonwealth’s design criteria and requirements and recommended that it should be adopted. The Commonwealth accepted the recommendation, noting that its subject matter experts had been deeply involved in all aspects of the design process including model testing and results analysis. At key stages during the study the Commonwealth provided comment and direction to ensure that the desired outcome was achieved.
Four-Bladed Propeller Procurement
The new four-bladed propeller design was of a monobloc configuration to accommodate the extra blade on the hub, as the fundamental dimensions of the hub could not be changed. (Note: With the original 3-bladed design, blades were bolted to the hub). The Commonwealth contracted Navantia to produce the manufacturing drawings for the propellers, obtain the appropriate LR class approvals and to procure three new propeller sets, one for each ALHD and a spare set. It is worthy of note that each ALHD requires four propellers, each of which is physically different. While the design of the forward propellers is the same and likewise for the aft propellers, port and starboard pod shafts rotate in opposite directions.
In consultation with the Commonwealth, Navantia undertook a competitive tender process for the procurement of the new propellers. Three Australian industries and six international suppliers were requested to quote, noting there was a tight timeline for delivery to meet the scheduled five year dockings of the two ALHDs. A combined Navantia and Commonwealth team undertook a tender evaluation of industry responses and in early 2020 the contract for manufacture was awarded to Silla Metal Co Ltd., Busan, South Korea.
As a result of Covid-19 and the restrictions on travel to and from Australia, no Commonwealth or Navantia representatives were able to attend factory acceptance tests. However, LR was engaged for certification and acceptance against LR’s rule requirements, while Silla Metal provided regular high quality evidence of the progress of the production of the propellers. The first set for Canberra was delivered in August 2020 with the other two sets in December.
The new propellers were fitted to Canberra during her scheduled docking maintenance period in late 2020. Figures 3 and 4 show two views of the port propeller set.
Sea Acceptance Trials (SATs) of the 4-Bladed Propellers
Following the installation of the new four-bladed propellers to Canberra the ship underwent an extensive set of SATs in March 2021 to recommission the propulsion machinery and evaluate the performance of the propellers. LR TID conducted the propeller observations, hull pressure measurements, structural vibration surveys and CEPAC2 measurements. The measurement positions and trials procedures were identical to those used in 2017 so that a direct comparison and assessment of the changes of the structural response could be determined.
The Results
Structural Vibration: The installation of the four-bladed propellers resulted in a significant reduction in the level of vibrations present throughout the platform. The average reduction in levels was between 50 and 60%, with key facilities on 2 deck seeing the largest reduction at 82%. The measurements of noise and vibration for assessment against the requirements of CEPAC2 indicate compliance, noting that all vibration measurements were well below the maximum specified levels.
The quantitative assessment of the vibration levels confirmed the qualitative improvement in platform comfort observed by the ship’s company and personnel conducting the trials. The redesign of the propellers has been very successful in reducing the overall vibration levels in the ALHD, which can only enhance the life of equipment and systems fitted. The vibration levels now present in Canberra are considered to be normal, i.e. what one would expect for a vessel of this size and type.
Propeller Performance: Propeller observations recorded significant reductions in cavitation and in the case of some criteria, a total elimination. This improvement in performance when compared with the original three bladed design was in line with the reduction in measured platform vibration levels. The magnitude of the hull pressure pulses reduced by 52% and 29% for the forward and aft propellers respectively. There were no recorded observations of erosive cavitation.
The observations and measurements showed strong correlation with model tests conducted during the four-bladed propeller design study. The results support and justify the comprehensive methods used to investigate and remediate the excessive ALHD platform vibrations.
Conclusions
The excessive structural vibration levels that affected the ALHDs since entering service and attracted continuous adverse comments from the ships’ companies have been all but eliminated by the fitting of the four-bladed propellers. Canberra now provides her ship’s company and equipment with a level of background vibrations that will not adversely affect the performance of ship’s systems and personnel. The improvements seen in Canberra have greatly enhanced the overall performance of the platform.
Adelaide has been fitted with the new four-bladed propellers with SATs planned for late 2021.
Special Thanks:
While noting that many people participated in the work to identify and remediate the vibration problems with the ALHDs, the author would like to acknowledge the important contribution made by the following key individuals, without whom the success of this project would not have been possible:
Mr Bob Love CB, OBE, FREng, Rear Admiral RN (Ret’d) TaRP Program Manager
Dr James Forrest, DSTG; Mr Martin Grimm, DNE
Dr Kian Banisoleiman, Dr Peter Carden, Mr Crispin Fetherstonhaugh, LR TID
Dr Jie Dang, MARIN
Mr Arthur Pugsley, Navantia (Australia)
About the Author:
Phil Baldwin has extensive experience in marine engineering and specialises in investigating and resolving complex engineering problems. During 21 years in the Royal Navy he completed his artificer training and on promotion, read his BEng (Hons) degree at the Royal Naval Engineering College Manadon. He spent 10 years at sea which included his appointment as MEO, HMS Beaver. After a period of 16 months working for the Chilean Navy, he joined LR TID, based in London. During the next 5½ years he undertook worldwide multidisciplinary technical investigations of machinery problems and failures in a variety of platforms, ranging from small ferries to VLCCs and cruise ships to LNG carriers.
Migrating to Australia in 2003, he returned to naval work in 2006. As the engineering manager with Rolls-Royce Australia Services he was heavily involved with the amphibious platforms and tankers. With his deep understanding of the material status of these vessels, he played a key role in the early stages of the Rizzo Review. He was the technical lead for the development and delivery of the material recovery plans for these assets.
In September 2015, as an independent contractor to Defence, he was engaged by SEA 2048 (ALHD) Acquisition as their representative at Garden Island, Sydney. While managing warranty claims and providing specialise advice to the SPO sustainment and engineering teams he identified a number of challenging problems in need of remediation. With the formation of the TaRP he took on the role of the TaRP Chief Engineer and was the technical lead for propulsion related issues. He continues to provide technical support to the ACS SPO.